Cut the gasket 1/2″ to 1″ longer than needed, cutting the end squarely. Perform an air blowdown to clear the press of any remaining solution. Connect the press’s filtrate discharge outlet to the recirculation tank. Storage tank with enough capacity to fill the press and allow for recirculation—roughly 1.5 times the press’s holding capacity. Take note of the patched cloth’s location and inspect it on a regular basis until the cloth is replaced due to normal wear.
Clear Edge has automated sewing to produce bags that meet the most stringent tolerances when precision sewing is required, such as with the Diastar-type pressure filter. Polypropylene is widely used because it is resistant to chemicals and substances across the pH scale and has a maximum temperature resistance of up to 185 degrees Fahrenheit. Replace the liner pipe in its counterbore and tighten the locknut, making sure the pipe is perpendicular to the plate.
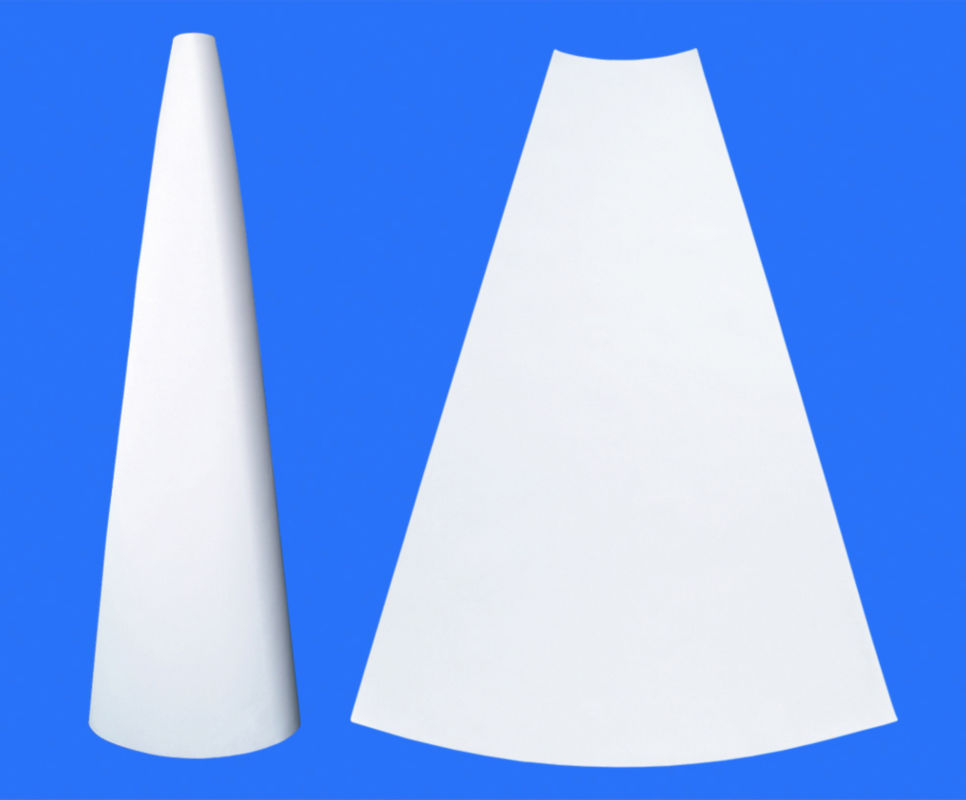
After the filter cakes are removed, the filter cloths must be washed before the process can be restarted. To clean the filter cloth, a high-pressure wash is commonly used, either with a pressure washer or an automated system. Depending on the location and size of the press, pressure washing can be done with one or two guns. To clean the filter cloth, an automated system uses spray bars with nozzles that go between each plate. Typically, automated filter cloth cleaning systems require 10 to 20 gpm and up to 1500 psi. Micronics is the world’s leading authority on filter press cloth, a critical component in optimizing your filter press operations.
Why You Should Replace Your Cloth Masks With N95 3-Ply Surgical Masks
The filter cloth may have been damaged if the mud cake does not agglomerate normally. Filter cloth should be replaced on a regular basis to avoid interfering with the treatment effect and subsequent processes. Great Lakes Filters and our Filpaco product line have a long history of supplying the industry with filter paper and cloth for a wide range of applications.
Furthermore, if temperatures are too high and cycles are too long, the Nordel elastomer may undergo additional cure, causing it to harden slightly. If the Nordel elastomer’s gasket life is inadequate, contact USFilter for a suitable replacement. Connect the acid pump’s outlet to the press’s center feed line.
Cloth Twill Structure
The twill structure is made up of multiple warp and weft structures that are connected in a row. Because the porosity is greater and the permeability is greater, the filter cake release efficiency will be greater than that of the plain lines. Monofilament yarn is composed of a single continuous filament of synthetic fiber.
We take great care in reviewing each customer’s process and application in order to design a filter cloth that is tailored to each customer’s exacting specifications. We will help you achieve drier cakes, optimal cake release, improved resistance to media blinding, and the filtrate clarity you require with Micronics Filter Press Cloth. Lamports regularly manufactures replacement filter cloths for any filter press, whether gasketed, non-gasketed, or plate and frame (drape-over cloths). Choosing the best filter press cloth for your application is no easy task. Filter cloth design and fabric selection necessitate filtration experts’ knowledge and experience.
If your process changes, we recommend that you re-evaluate your filter cloth for optimum performance. Place the filter plate for the cloth change in the gap’s center. Because of localized cloth wear, the risk of developing small holes increases as cloths age. Evoqua is your first and only stop for filter press cloths. Certain presses employ a cloth that “drapes over” the plates.