Screw presses and filter presses are two common types of dewatering technology. When compared to other dewatering equipment for a given application, filter presses produce the driest cake with the cleanest filtrate. The proper selection of cloths, plates, pumps, and ancillary equipment/processes such as precoat, cake wash, and cake squeeze is critical to the dewatering system’s optimal operation.
Clarifiers use gravity and polymers to cause solids to accumulate at the bottom of the tank, where they can be discharged as sludge. Because filter presses work with pressure, equipment that increases pressure via high-pressure technology is ideal for optimizing your filter press system. That is the secret to the success of MatecĀ® filter presses, which use pressures ranging from 21 to 30 bar to handle even the most difficult and difficult to treat slurries, regardless of industry or application. These distinguishing features help to explain why thousands of our filter presses have been installed around the world.
Filter Press Specification
Filter presses come in a variety of sizes, ranging from small, lab-scale presses to much larger capacities, such as those with 20002000 mm plates. In a single tank, you can thicken, clarify, mix, flocculate, and remove sludge. Remove surface contaminants from sand and other granular materials by deagglomerating raw materials. The Passavant FluX2-Press is a hybrid of the Passavant Flux-Drain Belt Thickener and the Passavant FluX-Press Belt Filter Press.
Ecologix provides a range of sludge dewatering filter press units with processing capacities ranging from 4,000 to 50,000 gallons per day. Elevated legs, plate shifters, platform roofs, pump controls, and a full line of accessories are available to customize your configuration. The Orege SLGTMsludge pre-treatment system, when installed ahead of an existing belt filter press or gravity belt thickener, changes the rheology of your sludge, allowing it to release water more freely.
The filter press works on the basis that liquid sludge is pumped between the filter plates, distributing solids evenly during the fill cycle. Filtrate flows from the filter plates into the drain manifold via the corner ports, yielding filtered water. The cycle is finished when the chambers are full, and the filter cakes are ready to be released. The filter cake falls from each chamber into a cake hopper or drum beneath the press as the plates are shifted. A dewatering cycle is initiated when conditioned sludge is fed into each recessed chamber at a sustained pressure of approximately 690 to 860 kN/m2.
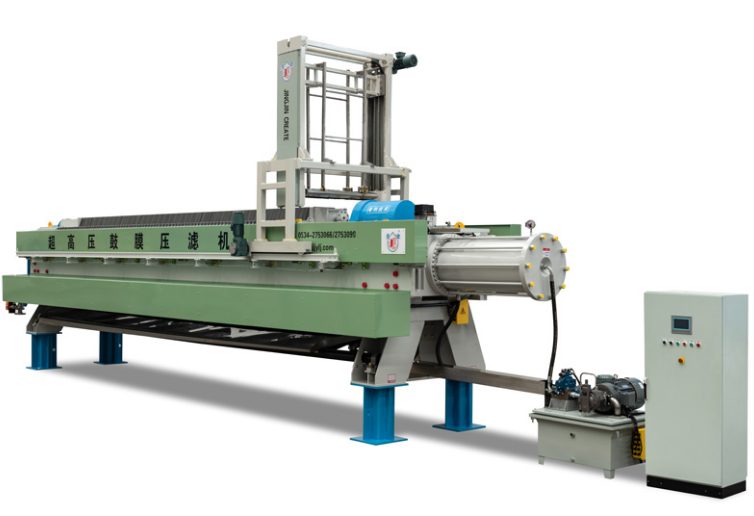
The cloths are made of monofilament, multifilament, or spun fibers. The smooth surface of monofilament fibers can aid in improving cake release properties. Because of the uniform circumference of monofilaments, fabrics with consistent pore sizes can be produced. Twisting several smaller diameter monofilament fibers together into a single strand produces multifilament and spun fibers. They are used to make fabrics with a very tight weave and fabrics where high flow rates are not required.
Filter Press Characters
This toughly constructed, fully automatic chamber and membrane filter press is dependable, fast, and provides high volume dewatering for the driest cake possible. Whether you require the high production capacity of an Overhead Beam Filter Press or the smaller Side Beam design, PHOENIX has a variety of customized options to meet your requirements. The HTBH belt filter press, which is widely used in a variety of industries, combines the thickening and dewatering processes into a single machine for sludge and wastewater. The HTB belt filter press, which is widely used in a variety of industries, combines the thickening and dewatering processes into a single machine for sludge and wastewater.
More information on the two types of clarifiers can be found on our Water Facts blog, Deep Cone vs. Rake Style Clarifiers. The recessed chamber filter plate reduces the possibility of clogging and plate damage caused by unequal pressure. China Environmental Protection Industry Association is the primary author of national standards for filter press and filer plates in China. The Jingjin filter press’s main beam is designed using welded box construction and manufactured using submerged arc auto welding technology.